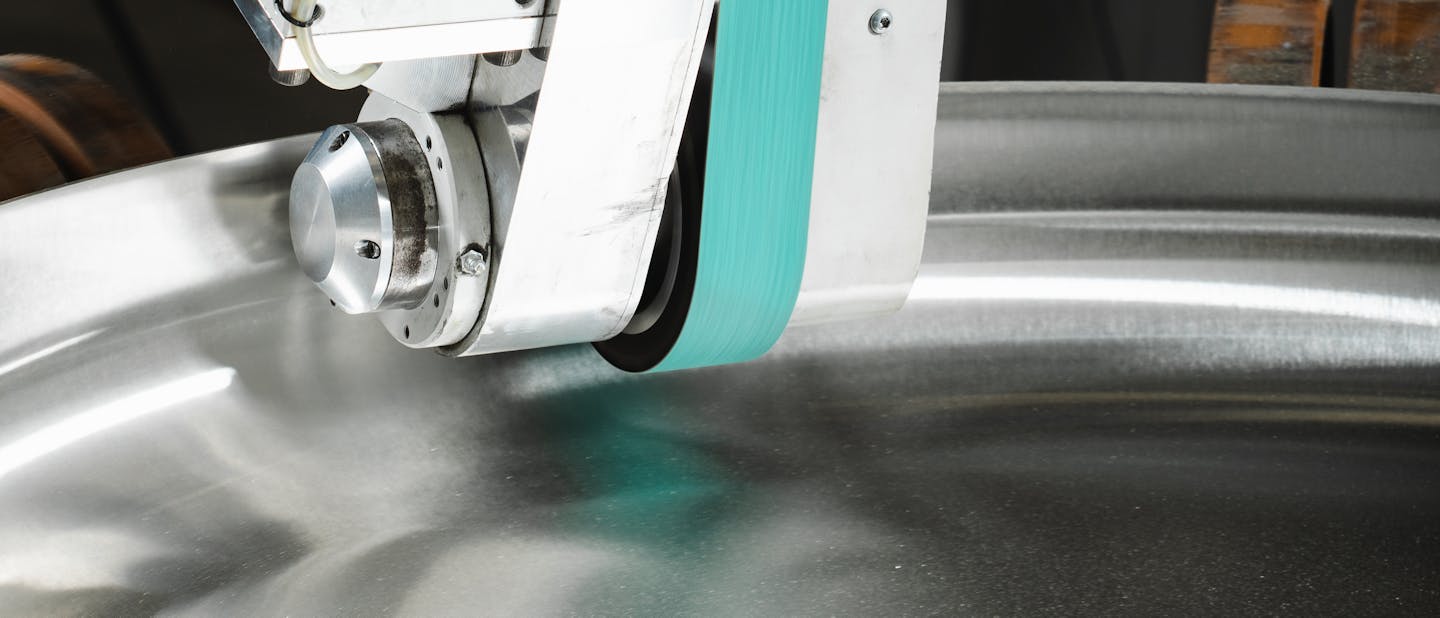
Achieving high gloss surface
Client challenge
Eurol's long-standing client faced a challenge in achieving high gloss on stainless steel plates used as part of a tank. The client sent these laser-cut workpieces directly to the polishing shop, which resulted in numerous problems. Hot-rolled stainless steel has many surface irregularities and pits that polishing alone cannot remove.
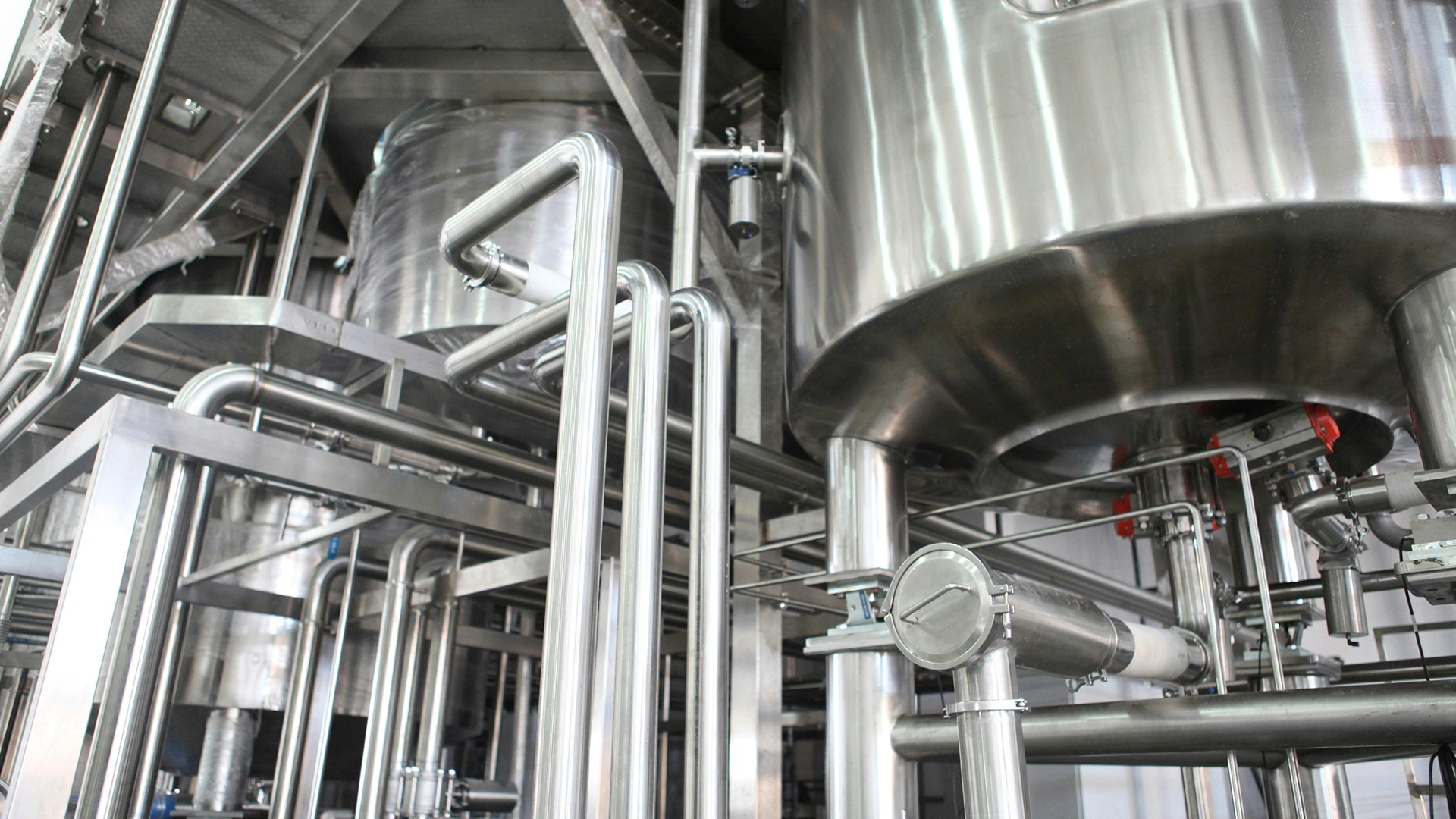
Eurol's approach
After careful consideration, Eurol produced test samples of abrasive belts and tested the grinding process on a Costa contact grinder. Starting with coarse grit and moving to increasingly finer grits, we achieved optimal smoothness. We used cloth-backed abrasive material for grinding stainless steel from grit 40 to 180. From 180 to 600, we used agglomerate. This is the latest innovation in grinding. Agglomerate belts have many advantages over conventional abrasive materials. They are used on contact grinders in cases where it is desirable for the belt to last as long as possible.
Grit | Type of belt |
---|---|
#40 | Hard cloth, zirconia |
#80 | Hard cloth, zirconia |
#120 | Hard cloth, zirconia |
#180 | agglomerate |
#240 | agglomerate |
#320 | agglomerate |
#400 | agglomerate |
#600 | agglomerate |
Agglomerate grains on the belts look very coarse, but these belts are intended more for fine grits. The abrasive grains are combined into a larger grain by a special process, so there are many abrasive grains in one grain, meaning there is a significantly higher number of grains per given surface area than on a conventional belt. Consequently, an abrasive belt with agglomerate grains grinds much longer, up to 5 times more. The image below shows the appearance of an agglomerate belt compared to a classic abrasive belt.
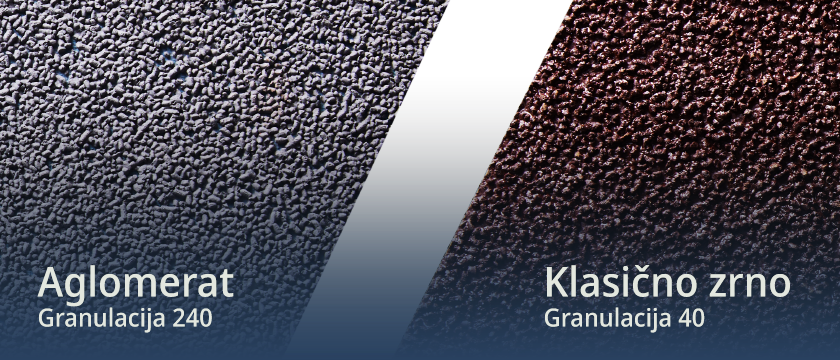
Issues during grinding
During grinding, we found that internal stresses in the material prevented the plates from being completely flat, which was a problem. The solution for uneven surfaces was to grind them enough to flatten them. This is a very time-consuming process. Another option was to flatten them mechanically with a milling machine. Grinding uneven surfaces is not smooth, making polishing such a surface very time-consuming. In addition, the workpiece got very hot at fine grits, so we used a water bath for cooling.
Findings and improvements
Despite the success, we found that the grinding process was too time-consuming and wasteful. After careful consideration, we advised the client to machine the plates with a milling machine after laser cutting. This allows for a flatter surface and requires less grinding. The milling machine leaves the surface very smooth, comparable to a surface ground with grit 180.
The client only had to grind from grit 240 up to 600. This means almost 50% saved in grinding and associated costs.
Conclusion and client satisfaction
The client was extremely satisfied with our final advice, as well as with the end result. The consulting and processing provided by Eurol significantly shortened the time and reduced the costs of processing.